Christmas is a great time for parents and kids to experience engineering with the inspiring cheerfulness of eating turkey, cakes, and looking at the fireplace while it's snowing outside. Offering the right gifts is a good way of bringing up the excitement that building artifacts can cause. While, of course, not all infants have the same thirst for scientific knowledge, for those which we find to have potential, the choice of technical gifts is not to be disregarded. While in my personal view, reminding myself as a toddler brings the memories of how vibrant and exciting it was to receive a chemistry kit, a microscope, an electronic device ready to be disassembled, etc, in the mind of a modern kid this might not be quite so satisfying. A Gormiti castle, a bunch of Ben Ten toys or any other sounding brands will certainly trigger more "processes" in a toddler's cognition.
A discussion about how today's television and toy industry affects children and youths is of little impact, but it is a fact that it is now in the hands of the parents and educators, to control the degree of exposure of their offspring to these elements, as the sole regulating factor seems to be profit generation alone.
Like with many other aspects of our world, let's hope some sense will grow out in the desert and guide those who deserve.
And of course Happy Holidays and fruitful engineering. Don't worry letting your kid become an engineer :)
Ad
Saturday, December 25, 2010
Sunday, December 5, 2010
Quadrature Encoder
One of the essential things an autonomous rover must have (which mine didn't had) is one or more quadrature encoders. In fact even some non-autonomous vehicles have these devices. Most regular cars these days feature this type of sensor as part of the ABS system (see http://en.wikipedia.org/wiki/Anti-lock_braking_system). Very reliable and high-resolution sensors can be found in these (featuring 90 steps or more).
For this autonomous rover I found that 16 steps would be the bare minimum, and easy to implement with common components.
As I didn't want to modify the RC car itself (drill holes, cut parts, etc), I looked for a solution that would minimize the impact on the car. As such I found that a good option would be to use the inner ring of the wheel as a surface for sticking an encoder band. This band has 16 steps, and looks like this:

For this autonomous rover I found that 16 steps would be the bare minimum, and easy to implement with common components.
As I didn't want to modify the RC car itself (drill holes, cut parts, etc), I looked for a solution that would minimize the impact on the car. As such I found that a good option would be to use the inner ring of the wheel as a surface for sticking an encoder band. This band has 16 steps, and looks like this:

Sunday, October 24, 2010
Now remotely controlled via IP
After some hobby time spenditure, the result meets the expectations. While it is a functional and simple (and a good fallback solution), controlling the car via a regular RC radio is not the most interesting scenario. Having a device that is mostly digital, being controlled by an analog receiver isn't quite the nicest thing one would want to showcase. With that in mind, and taking into account that all the necessary hardware was already there and working, I have decided to take a little bit of time implementing the necessary components to be able to control the car from a remote peer in a wifi network. As such all I had was to:
Thursday, October 7, 2010
Booster circuitry up and running
Running digital equipment has the drawback of requiring tight voltage ranges in order to operate. In the case of my robot, I had the need for powering the Fonera 2100 from a pack of 4 AA batteries. While the batteries can deliver 4.8 Volts once fully charged (which is barely sufficient to power this wireless appliance directly), once the voltage drops further, the Fonera ceasses to operate. In this situation the batteries still have remaining energy that is not possible to use.
Tuesday, October 5, 2010
Drastic Improvement: new Mobile Platform
After a lot of stress tests with the original platform, it was time for something better. The original platform was no more than a toy RC car (entirely made of plastic) with some hobby RC parts on top of if, such as refurbished steering system (with a real servo) and a home made ESC (Electronic Speed Controller) for the original toy car motor. During a demonstration with my 4 year old nephew, showing him how fast the roving robot would go in an open area, suddenly something happened: it started running full speed, totally out of control, both forward and backward (in my mind I immediately tought one of the ESC FET's had fried). I rushed to grab it, and suddenly smoke started coming out of the motor. Worried about the LiPo battery, with the motor still running and smoking, I centered all effort in disconnecting the battery. My nephew started to cry with the stange situation. After making sure no fire would occur, I had a confused infant to comfort.
Thursday, July 1, 2010
Power pack!
While the rear wheel traction motor provides plenty of power for normal operation, the curiosity of obtaining some extra power through a different propulsion method is appealing. Since I had some parts from a unfinished airplane project, the materialization of another exclusive idea became real: to build a special trailer for the car, with a single purpose - to push the car even faster, with the help of a propeller instead of traction wheels. Featuring a 9x6E propeller, a 150 Watt brushless motor, an 18 A ESC, and a 1300 mAh LiPo battery, this trailer provides the closest one can ever get from raw rocket power, with controller propulsion.
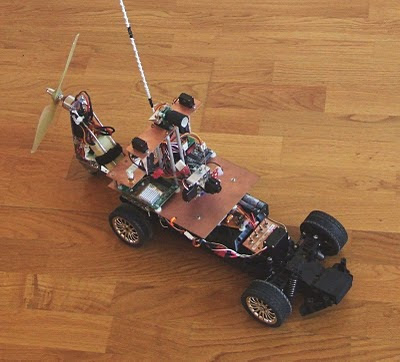
Wednesday, June 2, 2010
Sensors are never too many
While it is important to design a autonomous rover capable of performing even under the worst conditions and with the least available information from the surrounding environment, if we can provide good information, it will certainly lead to better results as long as we have a good software implementation behind it.
Tuesday, May 4, 2010
System override
Unlike some other domains, with robot software bugs can have expensive outcomes. In order to avoid unpleasant mishaps, I have decided to implement a hardware solution for preventing software originated problems that could cause a calm, boring robot to become a runaway beast hitting hard against walls, people, animals and anything that is in its way. To achieve this I have built a PWM control source multiplexer:
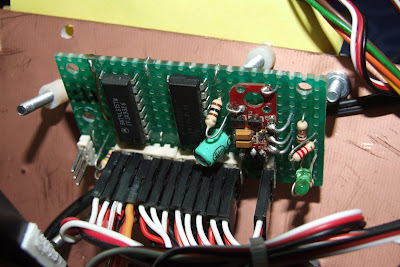
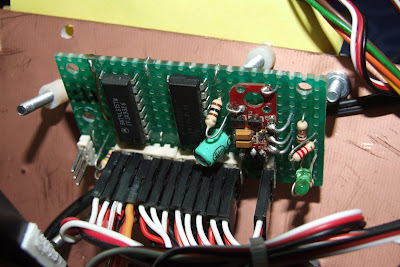
Sunday, May 2, 2010
Almost autonomous
With all the hardware prepared (except the quadrature encoder on the wheels, which is still to be implemented and installed), all conditions were met in order to be able to write some code and make the car finally move on its own.
I have first added the sonar module (the previously mentioned SRF02). This implied making a small aluminium support to fixate the sonar to the servo, while still being able to slightly adjust the tilt:
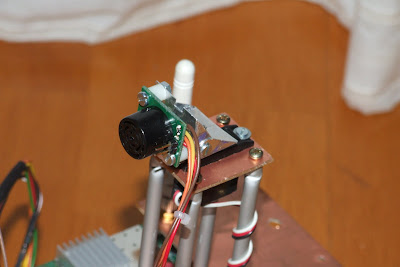
After installing it, made a quick check and read the ranging data directly through the MuIn original Windows application:
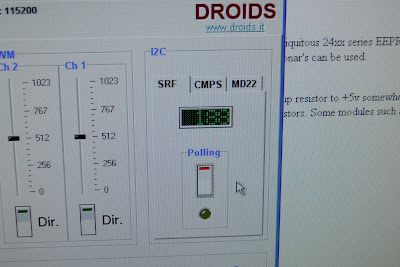
Every thing was fine. It was time to add more code to the MuIn PIC, implenting useful functions for the robot. A singe command returning both range data and the servo position would be useful, so I implemented it. It essentially consists of the following structure:
Each element is 8 bytes long. The PIC responds with the following answer format:
This allows a measurement to be taken, while the servo is sweeping.
A small video of the car in action:
I have first added the sonar module (the previously mentioned SRF02). This implied making a small aluminium support to fixate the sonar to the servo, while still being able to slightly adjust the tilt:
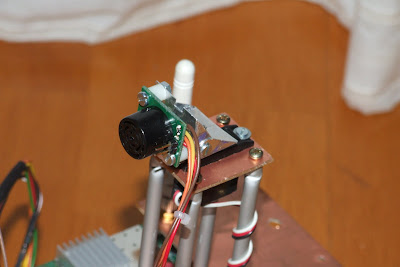
After installing it, made a quick check and read the ranging data directly through the MuIn original Windows application:
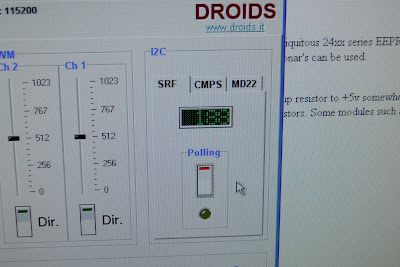
Every thing was fine. It was time to add more code to the MuIn PIC, implenting useful functions for the robot. A singe command returning both range data and the servo position would be useful, so I implemented it. It essentially consists of the following structure:
'@' | 'F' | 'S' | I2C addr | servo nr | 0 | 0 | '#' |
Each element is 8 bytes long. The PIC responds with the following answer format:
'@' | 'F' | 'S' | I2C addr | servo nr | Range HB | Range LB | Servo HB | Servo LB | '#' | Checksum |
This allows a measurement to be taken, while the servo is sweeping.
A small video of the car in action:
Sunday, April 25, 2010
More stuff on the pipe
The good work goes on, and the objective of achieving a fully autonomous rover is closing in. In this article I present 3 hardware additions:
First I found that the 1300 mAh LiPo battery could not be enough for long endurance roving activities. So I decided to add a pack of 4 NiMh AA batteries (2500 mAh each) dedicated to the Fonera. With this extra power, control and communications autonomy is guaranteed even if the powertrain pack becomes depleted. Additionally the efficiency is improved, because considering the fonera input voltage (5 V), and the voltage of the main pack (11.1 V), a regulator would be necessary, to properly drop the voltage. A linear regulator would not be a very efficient solution, and a switching regulator, in spite of being more efficient, is more complex and expensive. So with this separate pack, which provides around 4.8 V when fully charged, is enough for the Fonera (in fact the Fonera can be powered to a minimum of 3.5 V thanks to its internal low dropout regulator).
Thursday, March 25, 2010
Cognition on Wheels
Last, but absolutely not the least, is adding intelligence to the beast. Considering the budget constraints and simplicity of integration I decided by using a Fonera 2100 router as the workhorse for processing data. Equipped with a single chip Atheros solution, the integrated 32-bit MIPS R4000-class processor runs at 183.5 MHz, and is tipically enough for most network processing that is required. Additionally the IEEE 802.11b / 802.11g WiFi interface provides the means for remote communication with the vehicle. For local communication it features both an Ethernet interface, and a 3.3 V serial port.
Thursday, March 11, 2010
Let there be light!
One of the most pleasant situations is when can execute an idea without using any of your budget. It occured to me that having some onboard lightsource could be useful for the car, specially if you plan on doing night driving. Well I took a look at my repository of electronic junk, and found a pcb with 9 white leds from a broken flashlight, and a bunch of broken 9g microservos.
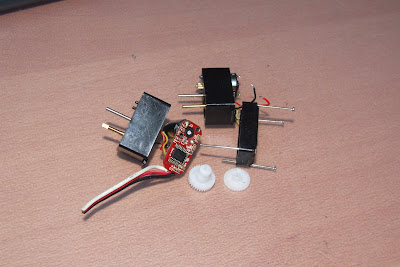
So I thought, well...if I could get the leds to be turned on and off through a free channel on my radio, it would be sweet.. And then took a look at one of the servos, and thought: I remove the motor, replace the encoder pot with a set of resistors, connect the leds in series with a small value resistor, and it should do the trick.
And so I did it: first analysed the servo operation in its original form. Connected the motor to an oscilloscope, and verified that a PWM signal that varies in duty cycle is fed to the motor. The further you move the stick, the more the duty cycle approaches 100%. Without surprise the peak voltage would be 5 V at the motor terminals (the same voltage that powers the servo).
Measured the pot resistance, which was 2 KOhm. Measured the current consumed by the leds while being fed with 3.1 V (minimum voltage for enough luminosity). It would draw 60 mA.
Then all I had to do was applying Ohm's law to find the appropriate resistor to drop the voltage, given the current that we know the LEDs consume. Found that the ideal value was 52 Ohms (V=RI <=> R = V/I <=> R = 3.1 / 0.060 = 51.66 ~ 52 Ohms).
I did't had this value (the closest resistor is 51 Ohms), so I used the closest resistor I could find at hand. Found a 47 Ohm, which in spite of being slightly smaller, it shouldn't harm the leds as I was being conservative with the voltage in the first place (these were being used in a flashlight powered by 3 AAA batteries - meaning that the voltage could be up to 4.5 V). The typical voltage to which white LEDs are rated is 4 volts.
With a bit of experimentation found an appropriate value for the resistors replacing the pot. One 2 K resistor between pin 1 and pin 3 of the pot terminal, and a 1 K resistor between pin 1 and pin 2.
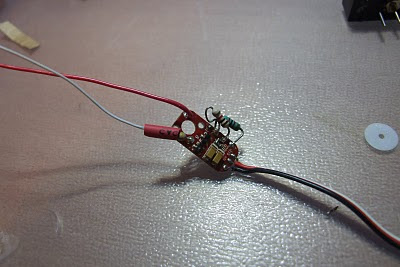
By doing this I trick the servo controller into thinking that the motor is always in the same position, while the user commands it to go to a different position. This causes the controller to continuously provide current to the motor, in an attempt to reach the desired position. Here instead of the motor we put the LEDs. The result is the LEDs being constantly lit while the stick is in a given region, and off in the remaining positions (because a negative voltage is fed to the LEDs - if a motor would be present instead, it would cause it to move in a different direction).
A little bit of soldering, and it was done! This way I had the cheapest possible RC headlight without spending a single cent.
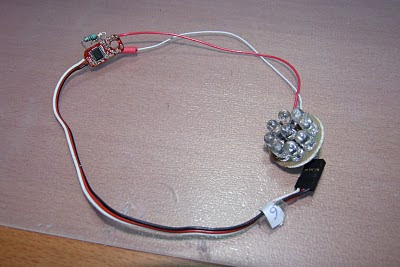
And finally, after putting heatshrink around the PCB, the work was done:
So I thought, well...if I could get the leds to be turned on and off through a free channel on my radio, it would be sweet.. And then took a look at one of the servos, and thought: I remove the motor, replace the encoder pot with a set of resistors, connect the leds in series with a small value resistor, and it should do the trick.
And so I did it: first analysed the servo operation in its original form. Connected the motor to an oscilloscope, and verified that a PWM signal that varies in duty cycle is fed to the motor. The further you move the stick, the more the duty cycle approaches 100%. Without surprise the peak voltage would be 5 V at the motor terminals (the same voltage that powers the servo).
Measured the pot resistance, which was 2 KOhm. Measured the current consumed by the leds while being fed with 3.1 V (minimum voltage for enough luminosity). It would draw 60 mA.
Then all I had to do was applying Ohm's law to find the appropriate resistor to drop the voltage, given the current that we know the LEDs consume. Found that the ideal value was 52 Ohms (V=RI <=> R = V/I <=> R = 3.1 / 0.060 = 51.66 ~ 52 Ohms).
I did't had this value (the closest resistor is 51 Ohms), so I used the closest resistor I could find at hand. Found a 47 Ohm, which in spite of being slightly smaller, it shouldn't harm the leds as I was being conservative with the voltage in the first place (these were being used in a flashlight powered by 3 AAA batteries - meaning that the voltage could be up to 4.5 V). The typical voltage to which white LEDs are rated is 4 volts.
With a bit of experimentation found an appropriate value for the resistors replacing the pot. One 2 K resistor between pin 1 and pin 3 of the pot terminal, and a 1 K resistor between pin 1 and pin 2.
By doing this I trick the servo controller into thinking that the motor is always in the same position, while the user commands it to go to a different position. This causes the controller to continuously provide current to the motor, in an attempt to reach the desired position. Here instead of the motor we put the LEDs. The result is the LEDs being constantly lit while the stick is in a given region, and off in the remaining positions (because a negative voltage is fed to the LEDs - if a motor would be present instead, it would cause it to move in a different direction).
A little bit of soldering, and it was done! This way I had the cheapest possible RC headlight without spending a single cent.
And finally, after putting heatshrink around the PCB, the work was done:
Wednesday, March 3, 2010
Intelligence on wheels
Robotic vehicles are not a novelty. Initial attempts to create autonomous roving machines date back to the 1970's, with examples such as Stanford cart in 1961 and Shakey, Moravec in 1979. These were simple machines. Digital computers were not yet miniaturized to the point of enabling interesting computing power onboard a vehicle, regardless of its practical size. Even so, the state of the art of the technology at that time proved sufficient to allow the mankind to explore new fronteers of a universe never before crossed by human artifacts. Two such examples were the NASA Voyager I and II missions. Having passed the 30 year mark in space, these prodigious machines still beam back health reports to earth, and should continue to be up and running until the energy generated by the plutonium based RTG (Radioisotope Thermovoltaic Generator)is insufficient to power the essential electronic systems onboard (of which one of the most important ones is the radio transmitter). This should occur anywhere in the next 10 years.
Today we have the result of tremendous technological improvements since the time the Voyager spacecrafts had been created. However, achieving the same degree of reliability is a milestone not always achieved in every case, regardless of how much extra knowledge the humanity have been gifted with.
While trustworthiness is not necessarily a consequence of innovation, it must be in the agenda, as long as the outcome is intended to be a dependable solution.
Anyway, the focus of this post is more on innovation itself rather than discussing trustworthiness and reliability. I am presenting a small part of what one day will be with us everywhere.
We are surrounded by automatic machines in our daily lifes. Even where it's less obvious. The small capsule called elevator, that takes us from one floor to another is one such example. While it doesn't look like a robot, it is a very autonomous machine. Equipped with clever microcontrollers, elevators are capable of making logical decisions, while multiple users request its attention. It's a simple example of a machine that in its current state of evolution is driven by an electronic computer, has sensors, and is capable of triggering actions (e.g.: activate a motor) based on a predefined plan, or in response to external input (e.g.: pressing a button). It can be enabled with useful optimizations such as having the ability to position itself automatically in different floors, depending on the selective demand at diferent times of the day, within a building.
Robots are intended to be useful for the human being, not to replace him. Through automatic machines we moved from one point to another in our ability to produce more and better artifacts, and to provide better services to people.
In this blog post I am presenting you with a machine that, while functional, is still the first step for achieving a helper robot, the hopefully will be the base platform for making very interesting household applications for machines this size.
I started from buying a cheap supermarket toy RC car. It called my attention the fact that besides its low cost, it was large (1:10 scale), had very nice looking wheels, and featured a 850 mAh 10 Volt lead acid battery (so most likely it also had a motor rated for 10 Volts or more):
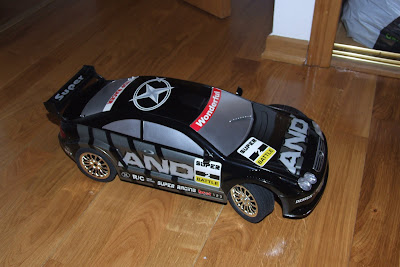
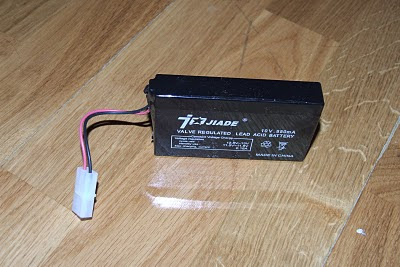
Of course the lead acid battery would not be very interesting as my future power solution, but we'll return on that later on. I decided to buy this car for the features managed to discriminate.
After fully charging the lead acid battery, I tested the car, still in its original form. I noticed that it really had nice torque and plenty of raw power. However, it lacked the ability to harness the beast. Like with most toy R/C cars, it's circuitry only allows zero or full throttle to be applied, both in forward and reverse directions. This, of course besides being very limited, also translates to prematurely worn and damaged gears. On the other hand the steering was also very poor. It was also zero or full travel in both directions. Of course we cannot expect proportional controls for a 25 Euro car! Well, I tested the car for, say, 1.5 minutes, and the battery soon started to gradually drop the delivered power. I was admired, either the battery had very poor quality or the motor was an animal.
I decided to start the transformation. I had a few spare hobby R/C parts such as a few microservos, a Art-tech 41 MHz 6 ch. receiver used in model helicopters and planes and a 11.1 V 1300 mAh battery (the stock battery from my Falcon 3D heli).
I started by removing all the crap out of the car, until I got this:
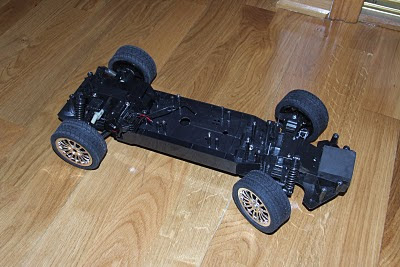
Here is the circuit board with the receiver and motor control. Here I had already removed the two SPDT relays used for reverse. Take a look at the big resistor (feer):
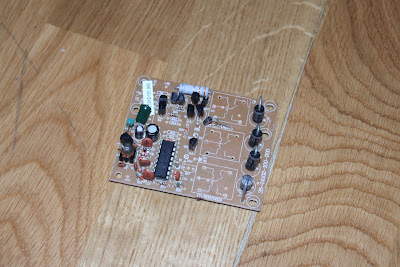
The original steering motor:
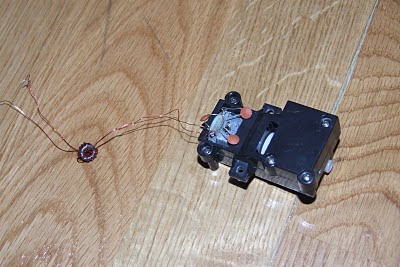
It hardly had torque to turn the wheels, specially after 1 minute of battery use.
The transmission motor yes, had quite a punch. I measured it's current while connected to the fully charged battery, it draws 1.5 A free running, and 13 A under full load (zero RPM on the shaft). So it consumed 130 Watts of power. The output power should therefore be around 100 Watts, assuming it's a reasonably efficient brushed motor.
I still needed a brushed motor ESC and better servo for the steering. I searched the web for DIY ESC solutions, and found this, which seemed interesting:
http://www.designsoft.com.au/ahome/rc/PIC-ESC/ESC.html
It featured design variations for both cars and planes. It seemed exactly what I needed, and I calculated that it shouldn't be hard to build and expensive. I had the option of choosing the relay or the H-bridge reverse. As I still had the two SPDT relays from the original circuit, I decided to try this version, as it would be slightly cheaper. Already in an advanced stage of the assembly:
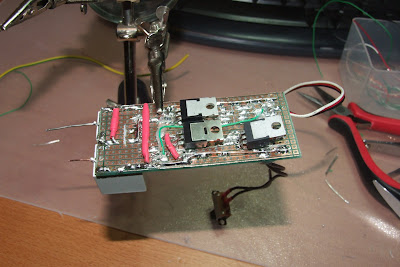
And the top view, with the two white relays:

After building the hardware it was time to program the PIC:
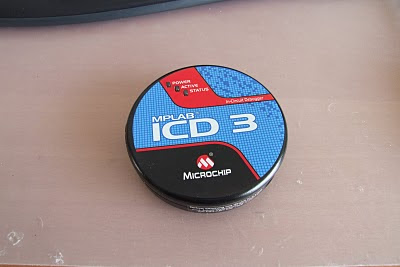
I had to build a small board with the ICSD socket for the PIC, as the ICD 3 is not provided with one:
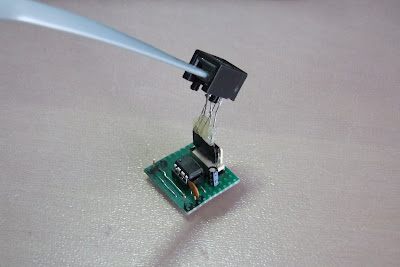
Mounted the 41 MHz radio and the LIPO battery. Both fitted nicely into the original
battery compartment:
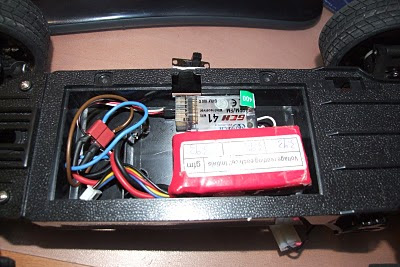
Mounted the 43 g standard servo (it has 6.5 kg of torque). Replaced the original links with ball links. Adapted the steering bar in order to attach the servo arm through a ball link:
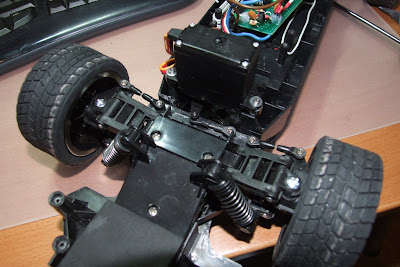
After a few more assembly iterations, mounted a virgin pcd board to be used as a plate for scientific instruments, and attached a gymballed support for a 1.2 GHz wireless camera. The gymball was assembled manually with aluminium. It uses two microservos to provide pitch and yaw for the camera. This is the result:
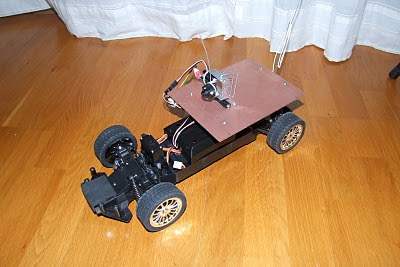
A detail view of the camera, which is also powered from the LIPO battery, through a regulator board I have also assembled (located in the bottom of the virgin pcb). It provides +5 V and +9 V necessary for the camera (camera and transmitter respectively):
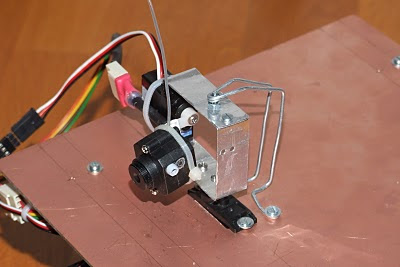
The car is then controlled by a standard PPM 6 ch transmitter (41 MHz):
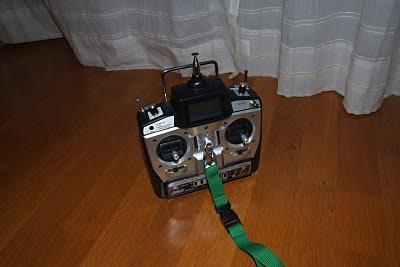
After the assembly, it was time for a test drive! Turned on the camera, connected the 1.2 GHz analog video receiver to a home made patch antenna, and time to hit the road..errmm...the wooden pavement..
As the car moved away from the place where I was controlling it, signal weakening and multipath interference became apparent. Some servos glitch violently under signal interference...dumb radio... The ESC on the other hand doesn't react because it properly filters occasional glitches.
Today we have the result of tremendous technological improvements since the time the Voyager spacecrafts had been created. However, achieving the same degree of reliability is a milestone not always achieved in every case, regardless of how much extra knowledge the humanity have been gifted with.
While trustworthiness is not necessarily a consequence of innovation, it must be in the agenda, as long as the outcome is intended to be a dependable solution.
Anyway, the focus of this post is more on innovation itself rather than discussing trustworthiness and reliability. I am presenting a small part of what one day will be with us everywhere.
We are surrounded by automatic machines in our daily lifes. Even where it's less obvious. The small capsule called elevator, that takes us from one floor to another is one such example. While it doesn't look like a robot, it is a very autonomous machine. Equipped with clever microcontrollers, elevators are capable of making logical decisions, while multiple users request its attention. It's a simple example of a machine that in its current state of evolution is driven by an electronic computer, has sensors, and is capable of triggering actions (e.g.: activate a motor) based on a predefined plan, or in response to external input (e.g.: pressing a button). It can be enabled with useful optimizations such as having the ability to position itself automatically in different floors, depending on the selective demand at diferent times of the day, within a building.
Robots are intended to be useful for the human being, not to replace him. Through automatic machines we moved from one point to another in our ability to produce more and better artifacts, and to provide better services to people.
In this blog post I am presenting you with a machine that, while functional, is still the first step for achieving a helper robot, the hopefully will be the base platform for making very interesting household applications for machines this size.
I started from buying a cheap supermarket toy RC car. It called my attention the fact that besides its low cost, it was large (1:10 scale), had very nice looking wheels, and featured a 850 mAh 10 Volt lead acid battery (so most likely it also had a motor rated for 10 Volts or more):
Of course the lead acid battery would not be very interesting as my future power solution, but we'll return on that later on. I decided to buy this car for the features managed to discriminate.
After fully charging the lead acid battery, I tested the car, still in its original form. I noticed that it really had nice torque and plenty of raw power. However, it lacked the ability to harness the beast. Like with most toy R/C cars, it's circuitry only allows zero or full throttle to be applied, both in forward and reverse directions. This, of course besides being very limited, also translates to prematurely worn and damaged gears. On the other hand the steering was also very poor. It was also zero or full travel in both directions. Of course we cannot expect proportional controls for a 25 Euro car! Well, I tested the car for, say, 1.5 minutes, and the battery soon started to gradually drop the delivered power. I was admired, either the battery had very poor quality or the motor was an animal.
I decided to start the transformation. I had a few spare hobby R/C parts such as a few microservos, a Art-tech 41 MHz 6 ch. receiver used in model helicopters and planes and a 11.1 V 1300 mAh battery (the stock battery from my Falcon 3D heli).
I started by removing all the crap out of the car, until I got this:
Here is the circuit board with the receiver and motor control. Here I had already removed the two SPDT relays used for reverse. Take a look at the big resistor (feer):
The original steering motor:
It hardly had torque to turn the wheels, specially after 1 minute of battery use.
The transmission motor yes, had quite a punch. I measured it's current while connected to the fully charged battery, it draws 1.5 A free running, and 13 A under full load (zero RPM on the shaft). So it consumed 130 Watts of power. The output power should therefore be around 100 Watts, assuming it's a reasonably efficient brushed motor.
I still needed a brushed motor ESC and better servo for the steering. I searched the web for DIY ESC solutions, and found this, which seemed interesting:
http://www.designsoft.com.au/ahome/rc/PIC-ESC/ESC.html
It featured design variations for both cars and planes. It seemed exactly what I needed, and I calculated that it shouldn't be hard to build and expensive. I had the option of choosing the relay or the H-bridge reverse. As I still had the two SPDT relays from the original circuit, I decided to try this version, as it would be slightly cheaper. Already in an advanced stage of the assembly:
And the top view, with the two white relays:
After building the hardware it was time to program the PIC:
I had to build a small board with the ICSD socket for the PIC, as the ICD 3 is not provided with one:
Mounted the 41 MHz radio and the LIPO battery. Both fitted nicely into the original
battery compartment:
Mounted the 43 g standard servo (it has 6.5 kg of torque). Replaced the original links with ball links. Adapted the steering bar in order to attach the servo arm through a ball link:
After a few more assembly iterations, mounted a virgin pcd board to be used as a plate for scientific instruments, and attached a gymballed support for a 1.2 GHz wireless camera. The gymball was assembled manually with aluminium. It uses two microservos to provide pitch and yaw for the camera. This is the result:
A detail view of the camera, which is also powered from the LIPO battery, through a regulator board I have also assembled (located in the bottom of the virgin pcb). It provides +5 V and +9 V necessary for the camera (camera and transmitter respectively):
The car is then controlled by a standard PPM 6 ch transmitter (41 MHz):
After the assembly, it was time for a test drive! Turned on the camera, connected the 1.2 GHz analog video receiver to a home made patch antenna, and time to hit the road..errmm...the wooden pavement..
As the car moved away from the place where I was controlling it, signal weakening and multipath interference became apparent. Some servos glitch violently under signal interference...dumb radio... The ESC on the other hand doesn't react because it properly filters occasional glitches.
Thursday, January 14, 2010
Ion Motor
Ion motors are very cool stuff. So cool that Nasa decided to invest research effort in this subject since the early 1960's when the physicist Harold R. Kaufman achieved the first design. In spite of the small ammount of thrust (when compared to conventional rockets), ion motors are capable of a very large exhaust speed, being equivalent to ten times the exhaust speed of a high quality rocket (the later can only achieve between 3-4 km/s). This means that ion motors are capable of continuously accellerating an object up to the exhaust speed (considering the space environment, where drag is practically absent). The time for exhaust speed to be reached depend of the mass being moved.
Subscribe to:
Posts (Atom)